Your Step-by-Step Guide to Printing Spectacular T-Shirts
There are several compelling reasons to get your personalized T-shirt produced. For example, if you want to advertise your new company or design your T-shirt, this article will help you. Estimating your quantity and budget, choosing a printing method, and selecting the proper fabric are some of the issues that will be discussed.
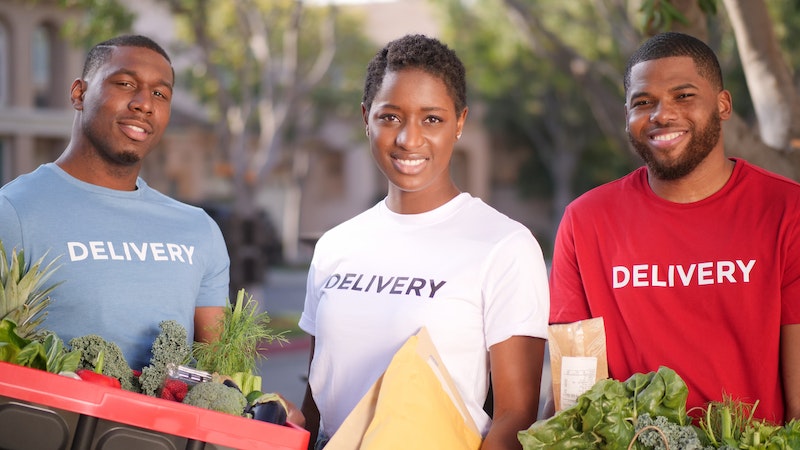
Make a Design
It is challenging to produce a T-shirt without a stunning design. To cut a long story short, make sure the design you choose expresses your narrative, is consistent with your brand, or just looks amazing. When creating a shirt, start by asking yourself what you want people to think about you or your company. Who precisely are you hoping to reach out to with this message? Spend some time developing a design that embodies the voice of your business, whether it be an artwork, a logo, a slogan, or any combination of the three.
Know Your Amount and Your Budget
Before you begin the printing process, determine your predicted quantity as well as your budgetary limits. When it comes to printing, a larger order nearly always results in reduced expenses for each item. It is advised that you purchase in bulk, especially if you want to sell the T-shirts.
In addition to establishing the quantity, you must also decide the sizes and the number of each. When printing T-shirts for your company’s items, keep in mind that some sizes sell better than others, but it is vital to always have a wide range of sizes available. Depending on the manufacturer, some dimensions may be more expensive than others.
Select a Printing Technique
When it comes to printing on a T-shirt and figuring out the best way to do it, there are many things to think about, such as the most common ways to print:
- Screen Printing. T-shirts with screen printing may be made by hand or machine. Whatever the result, this printing method has become the industry standard for T-shirt manufacture. The printer will convert your T-shirt design into original screens, allowing you to print in bulk.
- Vinyl Graphics. Transfer printing is a technique used to create graphics for vinyl T-shirts. Screen printing creates a unique look as well as a distinct texture; the finished product has a more daring and three-dimensional feel. Vinyl is often thought to last longer than ink.
- Direct-to-Garment. Direct-to-garment printing, or DTG printing, is a newer approach that makes use of the versatility provided by inkjet printing. The ink is applied to the fabric by spraying it on, similar to how inkjet printing is done on paper.
- Direct-to-Film. Direct-to-Film (DTF) printing, a contemporary T-shirt printing technique, utilizes the Epson F2270 DTF printer. With DTF, your T-shirt design is directly transferred onto a film, which is then heat-transferred onto the fabric, resulting in vibrant and detailed prints. This method offers a high level of customization and is gaining popularity for its ability to reproduce intricate designs with impressive clarity and color accuracy.
Select a Reliable Printer
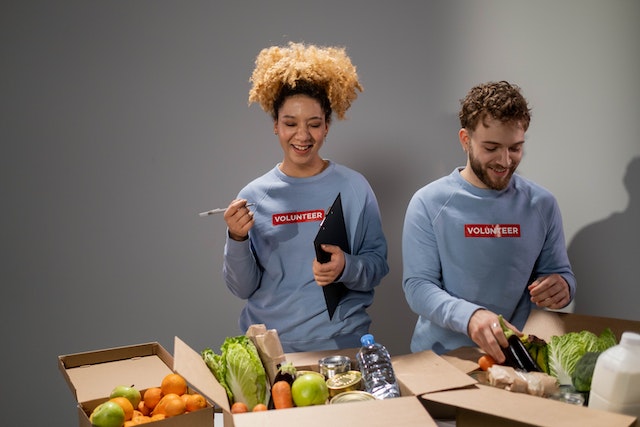
After you’ve decided on the layout, pricing, and printing method to use, the next step is to choose a printer. We highly advise spending some time exploring the numerous options available (both locally and online), since there is a huge range to pick from.
If you want to have your shirts printed locally, ask for actual product samples rather than just concept photographs. The majority of printing businesses welcome clients and visitors. Visit their shop to see and feel the art they’ve produced.
When selecting a printer, it is critical to keep your timeline in mind at all times to ensure that the order is done on time. When placing an order online, you must consider the time required for printing as well as the time required for shipment. If you are short on time, you may save time by placing your order locally and picking it up in person.
Choose a Fabric and a Shirt Style
To put it simply, T-shirts should be loose-fitting and comfortable. Keep this in mind when you evaluate various options for the fabric that will be used in your new design.
The T-shirt design depicts an otter with headphones and a laptop. A classic white crew-neck shirt with short sleeves is a traditional and good choice. One of the most popular options is one made completely of cotton. It may be worn in several ways and is also quite easy to clean. A cotton-polyester blend, which is generally less expensive than pure cotton, is a popular alternative that is both softer to the touch and more breathable.
Talk to your printer to find out which fabrics are best for the amount you need and costs you should pay as well as cosmos ink options.
Submit Your Files
When you’re ready to start printing, be certain that your printer has access to the design files you’ve produced. In person, ask your printer about the file formats, color specifications, and file sizes that they support. It is useful to inquire ahead of time to avoid any misunderstandings later on. Provide this information to your designer so that they may provide you with the final files on which they worked.
Review Your Sample
If you are purchasing in bulk, the printer should always provide you with proof of the shirt before it is manufactured. This is especially true for big orders. It might be a physical test print of the shirt or a digital proof of the garment. Because this is your sole chance to make any changes, you should go over everything thoroughly. Check that everything is in order, from the text to the numbers to the colors to the alignment. After that, you can proceed with the printing process.